Enhancing Productivity and High Quality Via Modern Metal Stamping Methods
As the demands for accuracy and performance proceed to rise, the combination of automation and electronic tools into the metal marking procedure has come to be paramount. By checking out the complex interplay in between technology, automation, and accuracy in steel stamping, a path towards unrivaled productivity and high quality guarantee unravels.
Advantages of Modern Metal Stamping
Modern steel stamping deals countless advantages in terms of performance, precision, and cost-effectiveness in the manufacturing sector. One of the essential benefits of modern-day metal marking is its capability to successfully create high quantities of intricate steel get rid of consistent top quality. This process eliminates the demand for several operations as it can do various jobs such as blanking, piercing, forming, and reeling in a solitary operation.
Moreover, modern-day metal marking allows suppliers to accomplish tight resistances and precise requirements, making sure that each part meets the needed standards. This high degree of accuracy leads to marginal material waste, lowered rework, and overall better product high quality.
In addition, contemporary steel stamping is a cost-effective manufacturing approach. The automation and high-speed capabilities of contemporary marking equipment cause lower labor expenses and faster manufacturing prices. This efficiency not only lowers manufacturing costs yet also enables business to fulfill tight production due dates and supply products to the market faster. Basically, contemporary steel marking deals a competitive edge to makers aiming to enhance productivity and high quality in their procedures.
Advanced Technologies in Metal Stamping
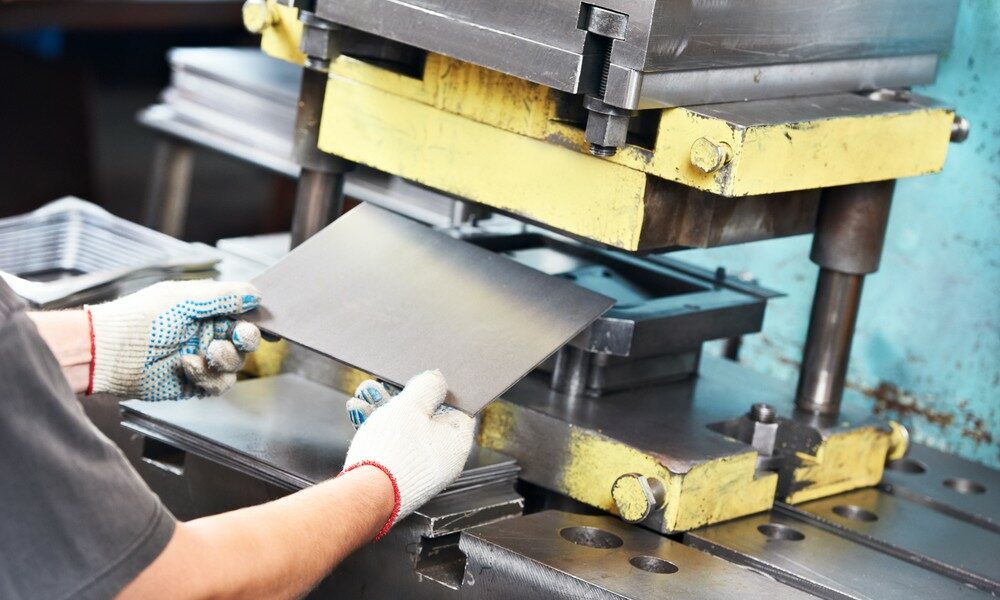
Another crucial innovation revolutionizing steel stamping is the use of servo presses. Unlike typical mechanical presses, servo presses use higher control over the rate and pressure applied throughout the stamping procedure. This control not only enhances the top quality of the stamped components but additionally minimizes material waste and power consumption.
In addition, improvements in simulation software have actually enabled suppliers to essentially check and enhance the marking process prior to physical production starts. This virtual prototyping aids identify possible issues early, resulting in set you back savings and faster time-to-market for new items. Generally, these advanced innovations in steel stamping are driving extraordinary levels of efficiency and top quality in the industry.
Improving Effectiveness Via Automation
The integration of automated systems has actually significantly improved the performance of metal marking procedures. Automation in metal stamping procedures supplies a myriad of benefits, including boosted manufacturing rates, enhanced precision, and lowered labor costs. By using robot arms and computer-controlled machinery, tasks that were formerly time-consuming and susceptible to mistakes can currently be executed quickly and with impressive precision.
Automated systems have the capability to deal with repeated jobs with uniformity, causing higher productivity levels and decreased cycle times. This boosted effectiveness not just leads to cost savings but likewise makes sure a much more structured and trusted manufacturing procedure. Additionally, automation permits real-time monitoring and data collection, enabling manufacturers to recognize and deal with concerns immediately, additional maximizing the total performance of steel marking operations.
Furthermore, automation promotes a safer working setting by minimizing the need for hand-operated treatment helpful site in unsafe jobs. By handing over these obligations to automated systems, workers can concentrate on even more facility and value-added tasks, adding to a much more efficient and productive workflow in the steel stamping industry.
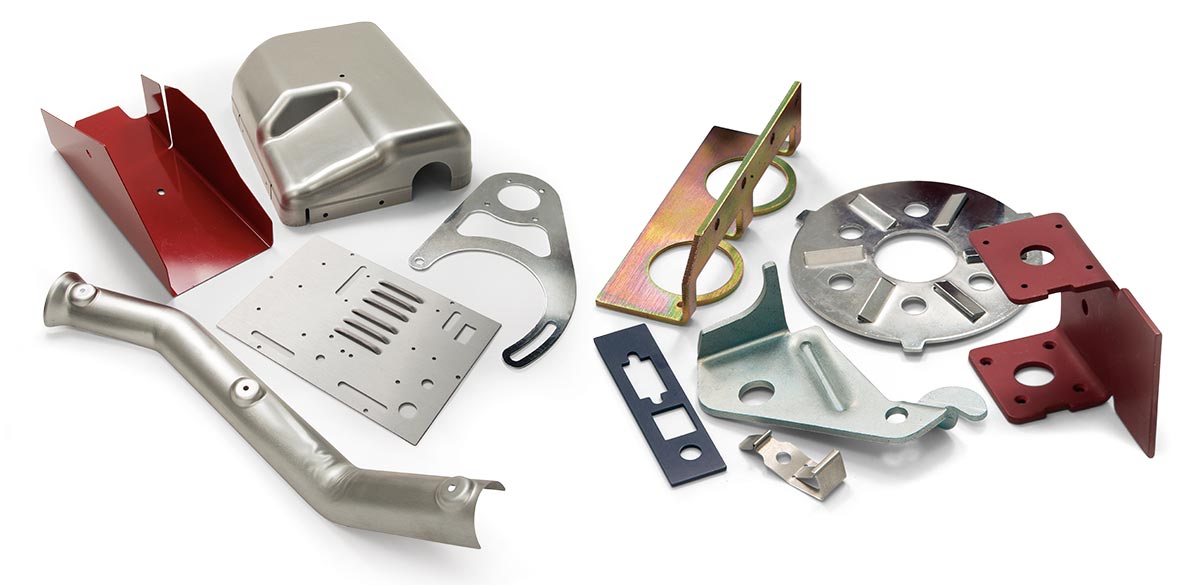
Quality Assurance Steps in Stamping
Implementing rigid top quality control steps is extremely important in guaranteeing the accuracy and uniformity of metal stamping procedures. One of the primary high quality control actions in metal stamping is performing regular evaluations throughout the manufacturing cycle.
Additionally, executing innovative modern technologies such as automated vision systems can even more enhance the quality assurance process by enabling real-time tracking and discovery of any anomalies during manufacturing. These systems make use of electronic cameras and computer algorithms to examine components with high accuracy and precision, decreasing the risk of defects leaving into the last item.
Additionally, establishing an extensive documentation system that tape-records quality assurance data and examination outcomes is crucial for tracking efficiency patterns and helping with continuous improvement campaigns. By assessing this data, producers can identify possible locations for optimization and carry out corrective activities to boost the general quality of their stamped items.
Enhancing Accuracy With Digital Tools
Employing electronic tools can significantly boost the precision of steel stamping procedures, reinventing the method manufacturers accomplish precision in their manufacturing. Digital devices such as computer-aided design (CAD) software application great site allow for the creation of detailed stamping layouts with exceptionally accurate dimensions. By inputting comprehensive specifications right into the software, makers can guarantee that each stamped item meets specific dimensional requirements, lowering errors and waste in the manufacturing process.
Additionally, the integration of sensors and real-time surveillance systems in stamping tools enables makers to closely keep like this an eye on the marking process and make instant adjustments to guarantee specific results. These digital devices provide beneficial data on variables such as stress, rate, and alignment, permitting fast identification and modification of any kind of deviations from the preferred requirements.
Conclusion
In final thought, modern-day steel stamping methods use countless benefits for enhancing performance and quality in producing procedures. By making use of sophisticated technologies, automation, quality control actions, and electronic devices, companies can improve effectiveness, precision, and total performance. These developments in metal stamping not only enhance manufacturing procedures yet additionally make certain consistent and top quality results. Accepting these contemporary methods can result in considerable improvements in the manufacturing market.